产品列表
简易高效的车架悬挂铆接线布置
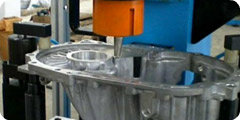
车架铆接是车架总成加工工序的一个关键环节,一条好的车架铆接线不仅要工艺布局合理,而且要安全可靠,加工环境良好,生产效率很高,这样才能给企业带来良好的经济效益。
汽车车架的作用是承受载荷,包括汽车自身零部件的重量及行驶时所受的冲击、扭曲、惯性力等。现有的车架种类有“边梁式”、“承载式”、“钢管式”等,我公司车架厂生产的车架为典型的边梁式载重车架,它由位于左右两侧的两根纵梁和若干横梁构成,横梁和纵梁一般由16Mn合金钢冲压而成,两者之间采用铆接或螺栓连接。
载重车架的铆接均采用液压铆接机,不论是大型汽车制造厂还是中小型汽车制造厂,均离不开液压铆接机,一条年产10~15万辆1~1.5t的车架装配线约需20~30个铆接点,而这些铆接点的合理分布
(即铆接机的合理布局)正是提高生产效率的关键。
简易高效的铆接线设计方案
为提升产能满足公司年产5万辆生产的纲领,我们决定利用原欧舒特车间南跨钢架改建成一条铆接线。为使新的铆接线建成后工位数量最合理,各工位加工时间能够接近均衡,我们对原车架铆接线现有两个主铆接工位在铆接过程中所花费时间进行了跟踪统计。以10个K29(99114510050)为例,第一工位主要将车架上左右纵梁及所有横梁总成、支撑板等零件进行装配并铆接部分铆钉,平均加工时间为15 min,第二工位将剩余小铸件及中间支座等进行装配,平均加工时间为25 min。单独对装配中间支座的时间进行跟踪测定平均时间为15 min。经过分析,我们决定建立铆接线时将原铆接线的二工位进行分解,在原二工位之前增加一个工位,让原来的二工位仅装配中间支座。这样一来,按理论分析, 10个K29车架的铆接在三个工位最长的加工时间应分别为15 min、10 min、15 min,可使原来25 min下线一个K29车架变为15 min下线一个,生产效率大大提高,产能也得到大幅度提升。
通过以上的数据分析,在新铆接线的这三个工位中将加工内容分配为:第一工位装配左/右纵梁总成及各横梁总成并铆接部分铆钉;第二工位装配剩余支撑板及其他小件并铆接所有未铆的铆钉、拧紧螺栓;第三工位专门铆接中间支座及拧紧螺栓。
该铆接线项目利用原欧舒特车间南跨钢架进行改建,非标设备改造情况比较复杂。从投资最少、改造工作内容最少、物流方向最顺及加工环境最开阔等多方面考虑,我们最终确定将铆接线的物流布置为从西向东进行。图1为该铆接线的工艺布局。
图1 新的铆接线的工艺布局
按照工艺要求,该铆接线共需XGM-16铆接发生器6台、标准铆钳4台、非标大号铆钳4台及170kg平衡器和140kg平衡器各4台。
车架在工位之间的顺畅运输是铆接线设计成功与否的关键因素之一,这其中既要考虑安全因素,又要防止吊运设备与铆钳悬挂小车出现干涉现象。因为原车架车间铆接线的小行车与铆钳悬挂小车共用16号工字钢,由于使用时间较长,工字钢出现变形,悬挂小车的滑轮也有磨损,工人在用小行车吊运车架时与近200kg的铆钳“叮叮咣咣”一同前进,有时还出现停止不前的现象。为解决这个问题,我们选用2t的环链葫芦,并用20号工字钢作为行走轨道。
环链葫芦最大的优点就是可以“东拉西拽”,最大倾角为15°,以车架前端宽度为940mm的车架纵梁用环链葫芦吊运至车架装配台上为例
(如图2所示),角偏移仅7°,因此选用环链葫芦在工艺方面不存在任何问题。
图2 环链葫芦吊运940mm宽车架纵梁至车架装配台的倾斜示意图
为解决葫芦与铆钳悬挂小车干涉的问题,我们特选用双层轨滑动悬挂小车,分布于环链葫芦两侧。线体布局剖视图如图3所示,双层轨滑动悬挂小车如图4所示。
图3 铆接线布局剖视图
图4 双层轨滑动悬挂小车
图4中,铆钳在悬挂小车下轨道16上左右运动,而下横轨16在上横轨4上可左右运动,这样一来等于增加了铆钳左右活动的尺寸范围,同时可兼顾780~940mm宽度车架的铆接,而且可以左右同时铆接,生产效率大大提高,且滑车内有球铰滑轮系统,工人在生产中左右拖动铆钳时也不费劲。为防止下轨道滑动时碰到电葫芦,另一方面也为了现场的整洁美观,我们在选用双滑动小车时使左右纵轨有50mm的高度差,横轨与水平面产生a倾角,铆钳在加工人使用完之后可自动复位。
计算论证及实施效果
钢架的强度及刚度是该铆接线设计的另一关键因素,因为该钢架原为F2000驾驶室总成所用,钢架允许所吊物重仅在0.5t以内,而车架最重在1.5~2t之间,故需对钢架进行改造加固,使其能承受2t的载荷,因此,如何将承受0.5t的钢架改造加固为能承受2t载荷的钢架成为需解决的焦点问题。经初步分析,我们决定在20号葫芦轨道工字钢上面用16号工字钢分段焊接加固,并为确定其加固后能承受2t的载荷特进行了力学理论计算。
对最大弯矩、截面惯性矩、抗弯截面模量、最大弯曲应力及最终强度、刚度的计算证明,加固方案实施后,4台2t的环链葫芦可同时在此钢架单跨内行走,无任何安全隐患,因此,此方案可行。
在工艺布局过程中,为节省空间,我们还考虑减少发生器,例如在第三工位,既能铆接尾梁又能铆接中间支座,因此在图1中,3、4液压站可选用一机 拖双钳的液压站,使有限的加工场地尽量开阔,给工人创造一个好的加工环境,也减少了很多安全隐患。
该铆接线在建成之后顺利投入生产使用,经现场跟踪测定车架加工时间符合最初理论分析,以K29车架为例,下线一辆份生产节拍由原来的25min提高为15min,生产效率提高了40%。双层轨动滑车与葫芦也没有出现干涉现象,双班日产车架也能达到50辆份以上。铆钳在使用完成之后能够自动恢复到原位,不会出现滑车碰撞葫芦的现象。目前,该车架铆接线正常使用没有出现过任何问题,为车架总成产能的提升起到较大作用。
对液压站布局的设想
通过此次铆接线的建设,笔者就液压站的放置问题也产生了一些新的想法。目前,国内许多载重汽车公司所使用的液压铆接机(包括我公司车架生产线)基本为每一支铆钳配备一台液压站,在一条较复杂的长线上一般设有20~30多个铆接点,相应地就有20~30台液压站,因而占去了铆接线两侧的大量空间,使工人的操作空间变得很狭窄,并且故障发生率也非常高。某些工厂把液压泵站架设在铆接线的上空,但这对泵站维护、保养带来了非常多的不便,尤其一旦液压泵站漏油则会影响到下方的正常作业,因此采取这种架空的分散供油型式并不是上策,同时也加大了投资。假若能在铆接线上搞“全线集中供油控制”,即在一条线上,数十个铆钳由一台液压泵站集中供油控制,这将是一个经济效益好、故障率少的更现代化的生产方式。采取集中供油后,其铆接点处只有一个液压集成控制阀,其占地面积也大大减少,同时可大大改善操作工人的工作环境。
联系方式
- 武汉埃瑞特机械制造有限公司
湖北省武汉市洪山区李纸路板桥南5号
邮编:430065 - 手机:13507127863
- 服务电话:400-027-0250
- 服务电话:027-88716898
- 传真:027-88716898
- E-mail:market@irivet.cn